Plum Maintance Management
Plum PMM is a comprehensive Maintenance Management solution that streamlines maintenance operations and provides the information needed to maximize the performance of assets, control maintenance costs and improve operations.
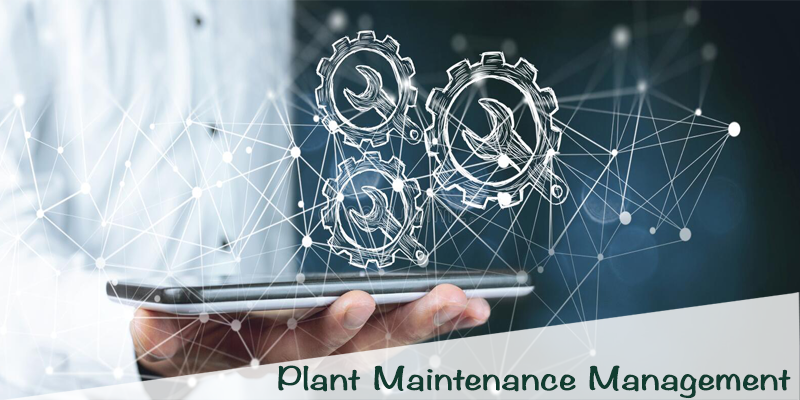
Plant Maintenance Management Module
Maximize Performance of Assets and Improve Operations
Plum PMM is a comprehensive Plant Maintenance Management solution that streamlines maintenance operations and provides the information needed to maximize the performance of assets, control maintenance costs and improve operations. Plum PMM can be tailored to meet the exact specifications of any maintenance, facilities or operations department and saves companies valuable time and money by better organizing, planning and managing maintenance activities. The results: less equipment downtime, greater return on assets, and improved efficiency, productivity and profitability.
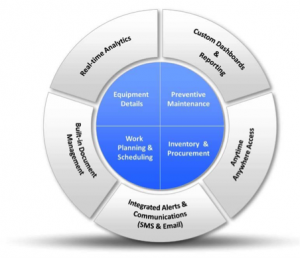
Plum PMM encompasses functionality for managing assets, preventive maintenance, purchasing and inventory control, planning and scheduling, asset history, cost tracking, condition monitoring and robust reporting in one user-friendly and affordable solution. This on-demand solution can be accessed across multiple locations from any browser based device (including Smartphone).
Key Features
Detailed equipment records form the foundation of Plum PMMS module. Equipment records anchor most maintenance tasks and activities. You need to capture different types of information about your assets along with how they are used, where they are located and whether they are in service. Quick access to equipment information directly impacts your ability to provide effective maintenance. This reduces the potential for introducing equipment failures while performing maintenance and saves time searching for the proper information. The ability to view equipment assemblies, sub-assemblies, components and parts is important to maximizing asset performance and improving technician wrench time by eliminating time spent searching for parts.
Preventive Maintenance (PM) module provides a single platform to easily plan, organize and manage all your PM work including building PM Master Plans, linking them to equipment and scheduling PM work order generation. PM module also provides a comprehensive audit trail of all PM work and reports schedule compliance.
- • Create PM plan for any equipment based on defined frequency or specific meter readings
- • Automatic PM task assignment with lead time for scheduling
- • PM roll-up for daily, weekly, monthly, quarterly and annual PMs
- • Integrated to inventory and procurement modules for automatic management for parts consumptions and requirements
- • Built-in document management to aid in defining PM tasks and procedures
- • Customize dashboards for specific management command and control requirements
Work Planning and Scheduling focuses on getting the right skills, parts, tools, appropriate instructions, permits and safety procedures together when the equipment is available. Maintenance schedules can be used to improve collaboration between operations and maintenance by mutually reviewing schedules and agreeing on the work to be done.
Plum PMM provides multiple features to streamling the planning and scheduling operations.
The integrated production module facilitates the user to define bays, machines, and view the current work load on this machine for various jobs.
- Define Plants
- • Define Locations / Bays
- • Attach Layout
- • View Workload
Once integrated with the PlumERP Production Scheduling Module, the application extracts the applicable machine productivity data from the machine loading and the associated input and outputs.
- • Machine Wise
- • Order Wise
- • Job Wise
- • Time Wise
- • Maintenance Slots
This single window provides the over view of the machine under reference by providing all required information of the specific machine.
This single window provides the over view of the machine under reference by providing all required information of the specific machine.
Plum Boards is a concept implemented across the PlumERP to view specific object and all its associated elements. This window picks all the data from different modules such as Warehouse, Production, Finance, Maintenance and Office Documents.
- • Machine Details
- • Material Consumed
- • Repairs Done
- • Movements
- • Inputs / Outputs
PMMS spare parts inventory management module tracks and optimizes your inventory as part of an integrated Enterprise Inventory Management System designed to get the right parts to the right place at the right time to maximize asset performance, optimize stocking levels and improve inventory service.
- • Multiple ware house and multiple bin support
- • Stock, non-stock and repairable item management
- • Inventory item allocation and reservation for work orders
- • Interchangeable and substitute part identification
- • Complete transaction audit trails, inventory valuation, balances, and usage levels
PMMS is integrates Maintenance Repair and Operations (MRO) purchases into enterprise level Procurement Management system. PMMS supports MRO purchasing and reduces overall procurement time and effort 50% or more with electronic requisitions and approvals, streamlined PO issue and expediting. PMMS purchase order tracking feature monitors purchase orders from creation and issue to delivery and payment.
- • Supports purchase orders, change orders, blanket orders and service orders and electronic POs
- • Automated requisition generation for stock item replenishment
- • Manages supplier information including minimums, terms and conditions, contacts
- • Quick and easy approvals with limits and controls
- • Complete audit trail of reviews and approvals
Attach all applicable documents for specific machine like maintenance documents, spares and other drawings pertaining to the jobs and fixtures. The attachments may be any electronic documents like the images, Excel, Word or PDF documents.
Analytics helps customers manage their business process and evolve toward best-in-class maintenance organizations. PlumSoft customers receive an interactive analytics foundation and tools to create, configure and manage integrated visualizations of Plant Maintenance data that is crucial in facilitating the continuous improvement of their maintenance operations.
Leveraging the easy to use and robust Analytics platform, visualizations provide the ability to manage KPIs, trends, multi-dimensional and what if analysis and can be merged with relevant enterprise data from other departments. With the Analytics web access, organizations have anytime anywhere access to relevant and comprehensive data on desktop, tablet or Smartphone.